Fasteners and Machining: Enhancing Durability and Efficiency in Manufacturing
Fasteners and Machining: Enhancing Durability and Efficiency in Manufacturing
Blog Article
Introducing the Ins And Outs of Bolts and Machining Procedures for Optimum Performance
In the world of engineering and production, the choice of fasteners and the details of machining processes play a pivotal duty in identifying the best efficiency and longevity of an item. From the apparently straightforward job of selecting the best sort of bolt to the complicated accuracy machining strategies utilized, every action in this process needs thorough interest to detail. As we start this expedition right into the globe of fasteners and machining, we will certainly reveal the subtle yet essential aspects that can considerably impact the effectiveness and top quality of the last product, clarifying the usually overlooked elements that can make all the distinction in achieving optimum performance.
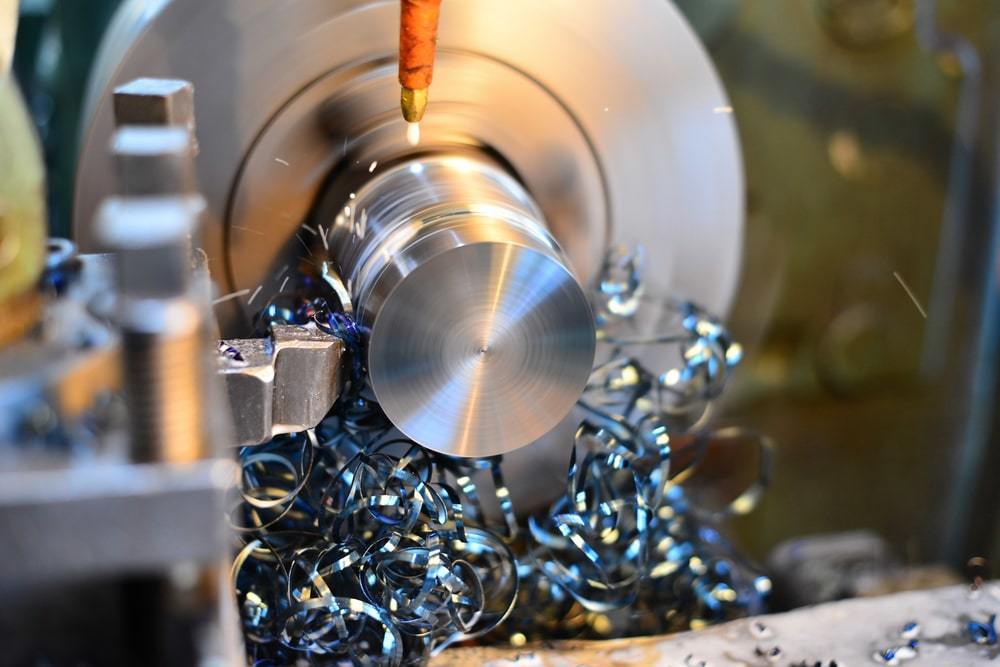
Relevance of Appropriate Fastener Selection
Choosing the proper bolts is vital in ensuring the structural honesty and durability of any kind of mechanical assembly. Bolts play an essential role in holding parts together safely, with the right selection contributing dramatically to the overall efficiency and integrity of the setting up. When picking fasteners, elements such as material compatibility, ecological conditions, load-bearing capability, and convenience of installment should be very carefully considered to guarantee optimal performance.
Improper fastener choice can result in a variety of concerns, including loosening, corrosion, and even architectural failing. Using bolts that are not fit to the specific requirements of the setting up can endanger its functionality and posture safety and security threats. Designers and engineers must carefully review the application needs and choose fasteners that meet or go beyond the needed standards and specs.
In addition, the proper bolt option process includes examining the joint style, prepared for loads, resonance levels, and possible thermal expansion or contraction to make sure that the picked bolts can hold up against the operating conditions successfully. By focusing on correct fastener choice, producers can improve the top quality, toughness, and performance of their mechanical settings up.
Types and Characteristics of Fasteners
A crucial facet of mechanical assemblies hinges on understanding the varied types and special qualities of bolts used in different commercial applications. Fasteners are vital parts that hold frameworks together, making certain stability and functionality. There is a variety of bolts offered, each created for details purposes based upon the application needs. Usual kinds of bolts consist of screws, bolts, nuts, rivets, washers, and pins.
Screws are threaded fasteners that are frequently utilized to join 2 or more components with each other. Nuts are inside threaded fasteners that mate with screws to hold elements together. Washing machines are thin plates that distribute the tons of a fastener, avoiding damages to the product being secured.
Recognizing the characteristics of each type of bolt is vital for picking the ideal one for a specific application, ensuring optimum performance and reliability of the mechanical assembly. Fasteners and Machining.
Accuracy Machining Techniques for Efficiency
The detailed layout requirements of different bolts demand employing accuracy machining methods for optimal effectiveness in producing processes. One of the primary strategies used in accuracy machining is Computer system Numerical Control (CNC) machining, which enables high levels of precision and repeatability in the manufacturing of fasteners.
By utilizing precision machining methods, makers can boost the quality of fasteners, decrease product waste, and enhance overall production performance. The use of advanced machining processes assists make sure that fasteners fulfill market standards and consumer expectations for performance and reliability.
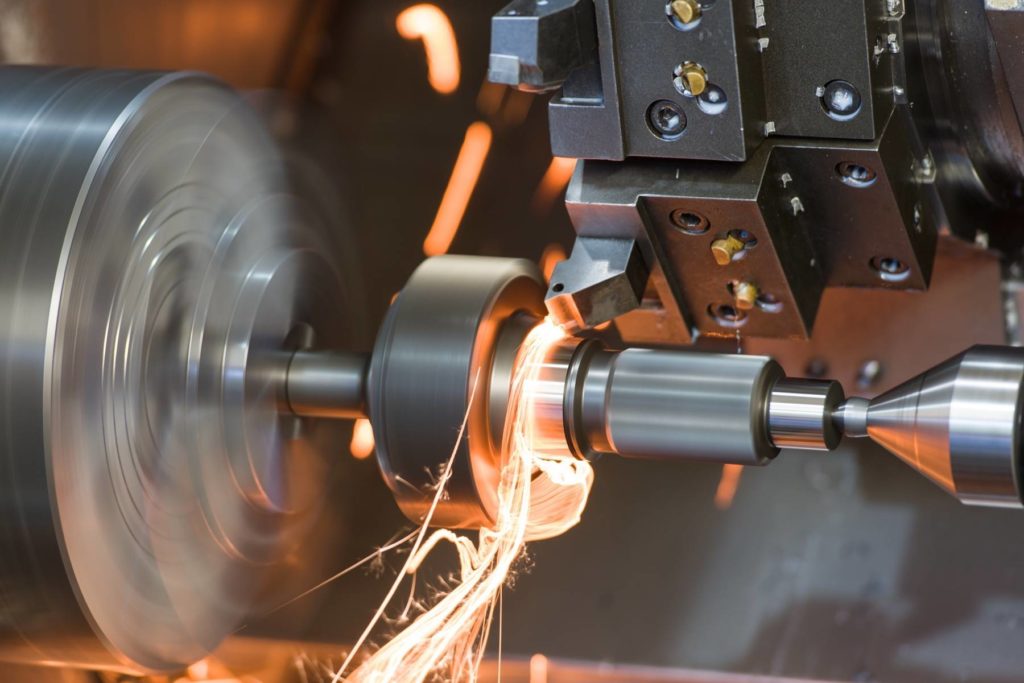
Variables Influencing Machining Refine Performance
Numerous variables play a considerable duty in determining the performance of machining processes in the manufacturing of fasteners. Enhancing these specifications based on the specific requirements of the bolt being created is essential to achieving specific and cost-efficient machining.
Device strength and stability also play an essential role in establishing machining process performance. A knowledgeable driver can make real-time modifications, troubleshoot problems successfully, and ensure that the machining her explanation procedure runs smoothly, ultimately influencing the last top quality of the bolt.

Quality Assurance Actions in Manufacturing
Factors influencing machining process performance, such as cutting tool option and device stability, directly impact the execution of quality control procedures in production. Normal upkeep of machining devices is additionally vital to support top quality control. By sticking to stringent quality control steps, suppliers can improve customer fulfillment, develop a track record for reliability, and inevitably achieve ideal performance in their machining procedures.
Final Thought
Finally, selecting the best fasteners and utilizing precision machining strategies are essential for optimal efficiency in making procedures. Understanding the kinds and features of fasteners, together with variables influencing machining procedure performance, can cause improved effectiveness and quality assurance procedures. By paying interest to these complexities, makers can accomplish greater levels of efficiency and dependability in their products.
In the world of engineering and manufacturing, the choice of bolts and the ins and outs of machining processes play a critical function in establishing the utmost efficiency and resilience of an item (Fasteners and Machining). One of the key methods used in accuracy machining is Computer system Numerical Control (CNC) machining, which allows high levels of accuracy and repeatability in the manufacturing of fasteners. The use of innovative machining processes assists make sure check my reference that bolts satisfy sector standards and client assumptions for efficiency and integrity
In conclusion, selecting the ideal bolts and utilizing accuracy machining discover this strategies are necessary for optimal performance in making processes. Comprehending the types and features of fasteners, along with variables influencing machining procedure efficiency, can lead to improved effectiveness and top quality control steps.
Report this page